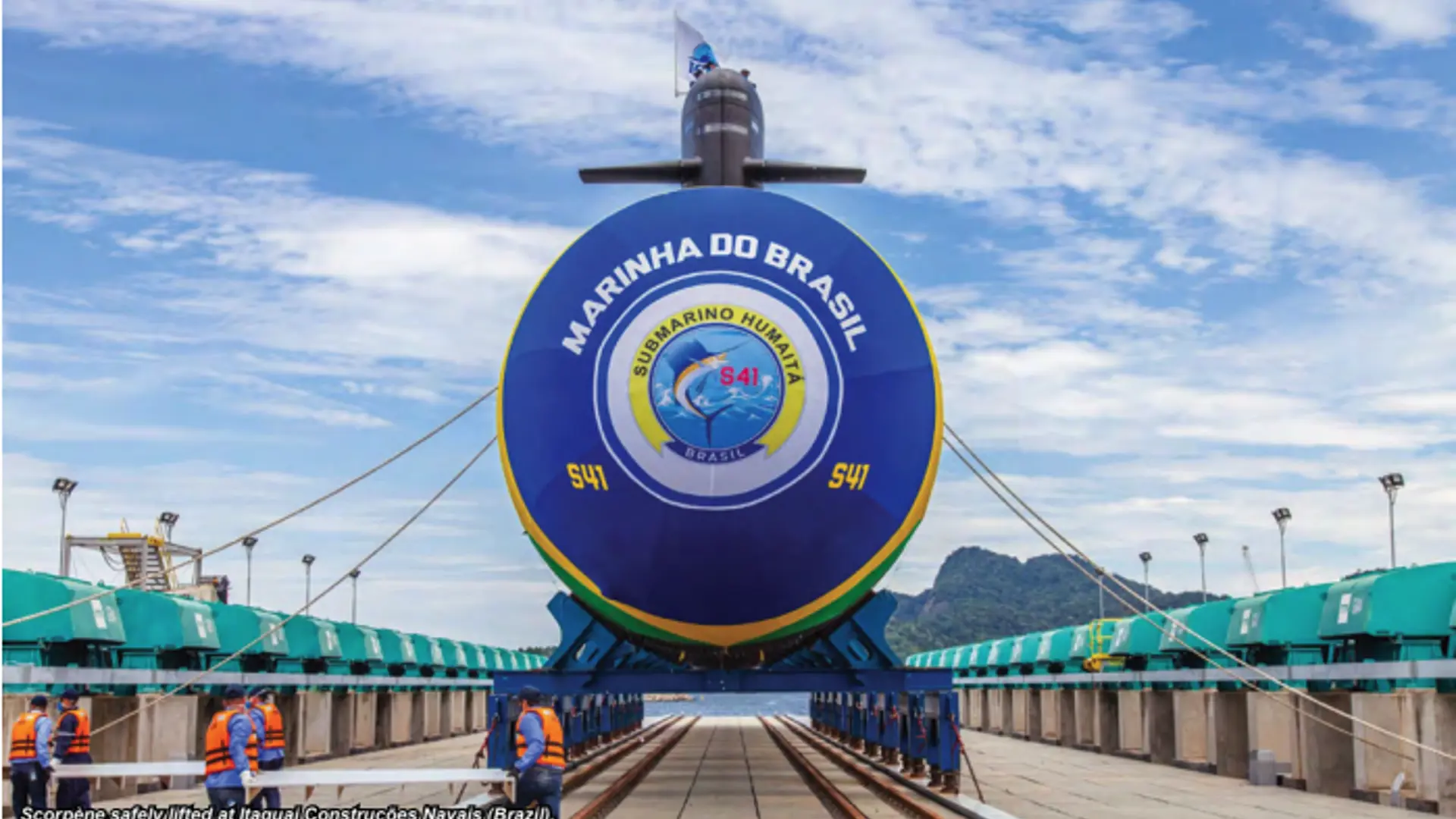
The innovative Shiplift Market Leader
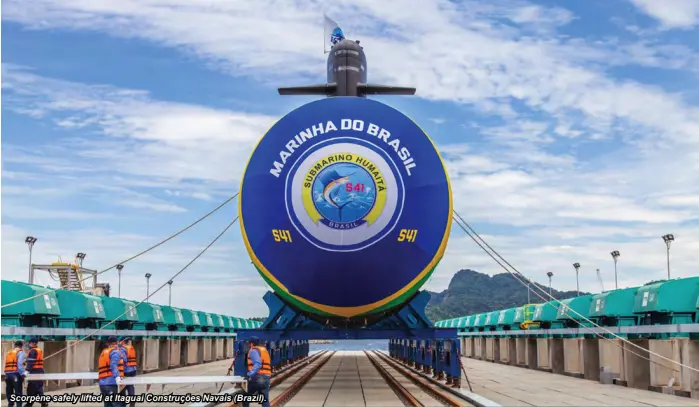
Introduction
Syncrolift AS specializes in designing and building turn-key solutions for docking and undocking ships in a safest and most efficient manner.
Headquartered in Vestby, Norway, Syncrolift® is part of the Norwegian Nekkar Technology Group (listed on the Oslo Stock Exchange), comprising a number of other innovative technology companies focused on developing disruptive technologies for offshore, windfarms and fish farms markets. With Syncrolift shiplifts and transfer systems, multiple vessels can be berthed ashore simultaneously for easy access, efficient repair and maintenance works in an environmentally safe work area and away from the waterside.
Syncrolift continuously innovates docking technologies to make dockings safer, faster and more cost efficient.
With more than 280 Syncrolift® systems installed worldwide, Syncrolift AS is the undisputed market leader, not only on newly build facilities, but also by providing maintenance services, upgrade solutions and modernization of drive & control on existing Syncrolift®’s, significantly improving safety, increasing nominal lifting capacities and extending the lifespan of installations up to 50 years or more.
Our history
The first Syncrolift® - was installed in 1957 by a small family firm PECO in Miami Florida, which was purchased by Northern Engineering Industries (NEI) back in 1979 and renamed as NEI Syncrolift Inc. in 1986.
In 1989 NEI merged with Rolls Royce plc and the Syncrolift division became part of Rolls Royce North America (RRNA) which was renamed later as Syncrolift® Inc. In 2015 RRNA sold and transferred all its Syncrolift® assets (including trademark, IP, patents, project design data etc.) to Syncrolift AS.
Today Syncrolift AS continues to be the OEM for every one of the 283 Syncrolift®’s which have been contracted since 1957 and successfully provide services (spares, inspections, maintenance support, upgrades and training) to most of the Syncrolifts installed world-wide.
Note: US company Pearlson Shiplift Corporation (PSC), which is founded only in 2008, is illegally claiming to be the OEM for the Syncrolifts. PSC has no business relationship with the old Pearlson Engineering Company (PECO).
References
Syncrolift provides turnkey solutions for dry docking of mega-yachts, commercial and naval vessels up to, and in excess of 30,000 tons.
Syncrolift is today the only shiplift supplier with experience in design and supply of shiplift & transfer solutions for handling submarines (various types, including nuclear powered submarines).
Apart from five recently newly built submarine lifts (Brazil, Peru, Malaysia, Pakistan and South Korea), Syncrolift is currently executing new submarine lift contracts in India and Indonesia (PT PAL). Syncrolift has also designed and delivered the new electro-hydraulic fluid bed rail based bogie transfer system for two US based submarine builders for the safe transfer of the US Navy’s nuclear submarines.
Syncrolift is the only company having performed the nuclear safety case for handling nuclear submarines in compliance with the UK’s Royal Navy standards for Barrows and Faslane nuclear submarine facilities.
Recently Syncrolift has also upgraded the submarine lift at Changi Naval Base (Singapore), which shall handle the new four TKMS built Invincible-class submarines.
New submarine Syncrolift® for PT PAL Indonesia
Also PT PAL Indonesia recently recognized Syncrolift’s technical excellence and experience on handling submarines and awarded Syncrolift with the contract for building their 6000 tons shiplift & transfer system for handling TNI’s existing and future (Scorpène) submarines.
Focus on Safety
Syncrolift is continuously focusing on further improving safety, efficiency and reliability of its products. By applying integrated (hybrid) shiplift platforms in combination with modern drive & control technology, Syncrolift has managed to maintain a zero-incident track record unlike other shiplifts operating with articulated platforms.
A wire rope breaking at a traditional shiplift fitted with an articulated platform may lead to a catastrophic loss of platform and damaging the vessel being lifted. Today more and more shipyards and naval bases decide to modernize their existing Syncrolift® with an upgrade, significantly improving safety and reliability.
Environmental friendly features
The latest Syncrolift® platform designs provide environmentally friendly features which allow shipyards to quickly execute hull cleaning, perform maintenance activities or emergency repair works while vessels remain on a locked platform.
Even contaminated wastewater is collected by the platform drainage system for pumping across to a suitable wastewater tank.
FastDocking solutions
In addition to the safe and efficient shiplift and transfer systems, Syncrolift® offer FastDocking tools for shiplifts, drydocks and floating docks, such as Propeller Pullers, Thruster Handlers, Side, Bilge &Tail Support Arms, Flex Pads, (automated) Vessel Inhaul & Positioning Systems, Auto Block Guiding Systems, which further reduce man-hours as well as docking times and increase safety.
Inhaul and positioning systems, enabling safe handling of vessels into and away from the dry-docking area. Auto block guiding systems, limiting the risk of misalignment of dock blocks in relation to the blocking arrangement of the vessel.
“With a current market share of more than 65%, we see our aggressive approach to improving and innovating our systems has worked out well”– says Managing Director of Syncrolift, Rolf-Atle Tomassen.
Global Service support & Syncrolift Academy
Syncrolift AS operates globally with service offices in Norway, Dubai, Miami, Singapore, Mumbai, and Perth. Our customers can count on 24/7 fast local responses by our regional service engineers or remote online by our Headquarter in Vestby, Norway.
Syncrolift has developed on site and in-house Lloyds certified training programs for dockmasters, operators and maintenance crew. By use of our Syncrolift® simulator, dockmasters and operators are trained on realistic docking operations and unforeseen situations.